Despatch offers a selection of benchtop, cabinet, walk-in and conveyor ovens that are ideal for curing applications. Despatch curing ovens offer fast ramping and cool down rates for maximum productivity, short cycle times and consistent, reproducible curing processes for all product loads.
Curing ovens are used for a variety of applications involving coatings, adhesives, rubber and thermoset plastics and composites. The electronics and semiconductor industries use Despatch clean process ovens for epoxy curing and polyimide curing. Despatch specializes in polyimide curing ovens that are designed to meet the unique process requirements for hard baking polyimide coatings in an inert atmosphere.
Despatch curing ovens are designed to provide tight temperature tolerance and precise control for repeatable results and uniform airflow that ensure proper curing across an entire load. The ovens are exhausted to effectively remove the VOCs given off during curing, ensuring a safe environment. Best-in-class energy efficiency is achieved with superior insulation and cabinet design as well as recirculating airflow management. Despatch offers gas or electric batch ovens for curing small to very large loads and conveyor ovens with multiple zones for continuous processing. If your process requires a custom solution, we can work with you to create a configuration that suits your specific needs.
Large Capacity Walk-In Ovens
The 476 and 952 cubic foot capacity Despatch TAD/TFD walk-in ovens feature uniflow airflow to ensure uniform temperatures throughout the oven. These large models are often used as the basis for composite curing systems with Focal Point Software and vacuum ports added. Maximum temperature is 343°C (650°F).
LEARN MORE
REQUEST A QUOTE
TA Composite Curing Oven
These walk-in ovens are designed for industrial process versatility, dependability and economical utilization of facility space. They are typically used for aging, curing, bonding, annealing, drying, baking and heat treating. TA Composite Curing Ovens offer customers a variety of beneficial features, including vacuum ports, lift doors, and tight temperature uniformities.
LEARN MORE
REQUEST A QUOTE
Vacuum Bagging and Pressure Control System
The Despatch composite curing system offers an integrated, multi-port vacuum system and jack panels to connect as many thermocouples as needed for monitoring the curing process. Mold preparation, including preheating, drying and cleaning processes, can also be provided.
LEARN MORE
REQUEST A QUOTE
Focal Point™ Process Control
Despatch composite curing systems are available with Focal Point™, an intuitive, PC-based process control system that is user friendly and easy to navigate. Focal Point™ fully controls the curing process and documents all process information, providing traceability and validation of part quality.
LEARN MORE
REQUEST A QUOTE
Composite Curing Brochure
Composite Curing Oven Technology
The anchor of the Despatch composite curing system is an oven that delivers exceptional temperature uniformity for perfectly cured parts. Multiple thermocouples are connected through jack panel arrays to fully monitor the part as well as the oven temperature.
- Flexible and customizable to specific composite curing requirements
- Tight uniformity, standard at +/-5°C or better
- Electrically heated or gas fired
- Custom airflow to optimize heat transfer to unique molds
Integrated multi-port vacuum systems
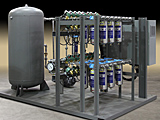
Out-of-autoclave curing requires a vacuum bagging system to apply pressure to the composite to eliminate voids. The Despatch vacuum system includes a vacuum pump and ports that can be added to suit your needs.
- Vacuum pump and all required components for complete system
- Vacuum monitoring with data recording throughout cure cycle
- Stringent vacuum stability tolerances less than 1 Hg loss per hour at 25Hg
Focal Point™ Process Control System
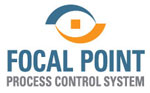
Tight process control and monitoring is critical for consistent quality parts. Focal Point™ fully controls the curing process and documents all process information, providing traceability and validation of part quality.
- PC-based system with Ethernet communication
- All relevant process data is saved on system PC and can be accessed from plant computer system
- Standard and customized reporting capability to validate process
- Vacuum and pressure system can be monitored and controlled from display
You may also be interested in: